VDA Battery module
VDA Battery Module is standardized battery module designed according to the specifications set by the German Association of the Automotive Industry (VDA – Verband der Automobilindustrie). These battery modules are an integral part of the battery system of an electric vehicle and have standardized dimensions, electrical specifications and safety requirements. Standardization is essential to drive the industry forward and improve efficiency, and the VDA standard for battery modules is an important milestone in the standardization of battery technology, providing a uniform approach to the design and manufacture of batteries for electric vehicles.
Now let’s take a closer look at the VDA Battery Module.
Table of Contents
What is a VDA Battery Module?
Initially, automakers hoped to achieve scale and reduce costs with the help of standardization of battery cells. But the needs of each automaker are different, the needs of different models of the same manufacturer are different, and battery companies have a very wide range of battery cell size specifications. So they turn to standardization of battery modules. Battery manufacturers then manufacture the right size battery cells according to the battery module requirements.
VDA stands for Verband der Automobilindustrie (German Association of the Automotive Industry). The VDA Battery Module Standard, developed by VDA, is a comprehensive set of guidelines that define specifications, performance requirements, and safety standards for battery modules for electric vehicles. These standards establish harmonized technical specifications for the entire industry, simplifying the supply chain and production processes and enabling interoperability between different manufacturers.
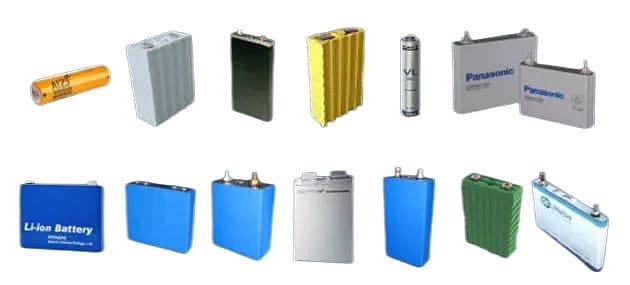
VDA battery modules are like Lego blocks for electric cars. Lego blocks are designed with standardized connections to ensure a perfect fit, regardless of the kit they come from. And so are VDA battery modules, which can be used regardless of the manufacturer they come from, as long as they are produced to strict standards.
The common VDA modules are VDA 355 module, VDA 390 module, VDA 590 module and so on. Different models of VDA modules are usually named by the length of the battery modules. For example, VDA 355 module refers to the VDA compliant module with a length of 355mm, and VDA 590 module refers to the VDA compliant module with a length of 590mm.
Basic Structure of VDA Battery Module
To understand the basic structure of a VDA Battery Module, it is important to first understand what a Battery Module is. Click here to learn more about it: What is a battery module?
Below are a few key components of the VDA Battery Module:
1.Battery Cells: Standardized lithium-ion battery cells arranged in series and parallel configurations. Attention should be paid to the arrangement and spacing between the battery cells to facilitate electrical connections and optimize thermal management.
2.Mechanical Components: Rigid structural frames that meet VDA dimensional specifications. With standardized mounting points for vehicle integration.
3.Electrical Components: With standardized high-voltage connectors, busbars, temperature sensors, etc.
4.Others: VDA-compliant communication interfaces, etc.
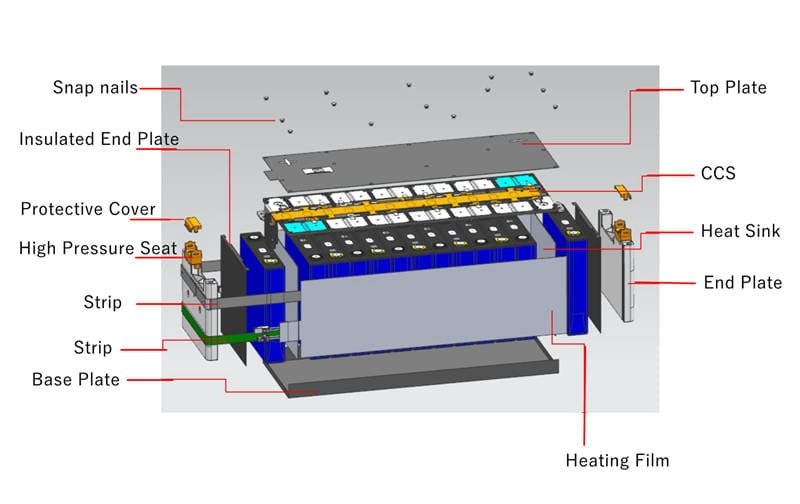
VDA Battery Module Advantages
1. Cost-effectiveness
The standardized design of VDA battery modules brings significant cost advantages to the whole industrial chain. In the production chain, the unified design standard enables enterprises to achieve large-scale production, significantly improving production efficiency and reducing unit costs. Standardized design also simplifies supply chain management, and the commonality of components not only reduces procurement costs, but also reduces inventory pressure. In terms of R&D, unified standards avoid duplication of development, and enterprises can focus their resources on product optimization and innovation, significantly reducing R&D costs and accelerating the speed to market.
2. Quality and Safety Assurance
VDA standards provide a guiding framework for quality control and safety of battery modules. These uniform standards help to ensure that the quality of products from different batches and different manufacturers is maintained at a consistent level. The VDA standards also emphasise the basic requirements of battery modules in terms of mechanical protection, electrical safety, etc., to ensure that the modules operate reliably under various working conditions, providing a basic guarantee for product safety.
3. Maintenance and After-sales
One of the most direct benefits of VDA standardization is the ease of maintenance. This standardized design makes modules interchangeable: both mechanical fixing points and communication interfaces, etc., follow a uniform design specification. This not only improves maintenance efficiency, but also reduces maintenance costs. For EV manufacturers, a unified module standard also simplifies spare parts inventory management and reduces inventory pressure on different module types.
4. Competition in the Marketplace
The VDA standardized modules offer a unique advantage in terms of competition in the marketplace. Products from different suppliers can be used interchangeably, which greatly increases the flexibility of procurement. For EV manufacturers, standardized modules facilitate cross-platform applications and simplify the system integration process. In addition, standardization also improves product iteration efficiency, enabling companies to respond faster to market demand and maintain a competitive edge.
Differences Between VDA Module and Traditional Module
1. Differences in Design Philosophy
Traditional battery modules are often designed to individual manufacturer’s specifications and therefore vary in design for a particular vehicle or platform. Each manufacturer develops its own unique mechanical structure, cooling system and electrical interface solutions. In contrast, VDA modules follow standardized specifications for all key aspects – from physical dimensions to interface design. This standardized approach ensures compatibility between different manufacturers and vehicle platforms.
2. Manufacturing Differences
Manufacturing of traditional modules often requires adapting production lines for different modules, sometimes with specialized tooling and equipment. This leads to higher setup costs and reduced flexibility. However, VDA modules use standardization to significantly reduce manufacturing complexity and achieve economies of scale.
3. Interface and Integration Differences
One of the most significant differences is in the interface design. Traditional modules have proprietary interfaces that vary from manufacturer to manufacturer, and even from model to model for the same manufacturer. VDA modules eliminate this complexity by standardizing interfaces.
4. Maintenance and After-sales Differences
The impact of standardization is particularly evident in maintenance scenarios. Traditional modules often require specific tools, procedures and spare parts for each module variant, which complicates maintenance and increases inventory costs. VDA modules simplify this process with standardized maintenance procedures and common spare parts.
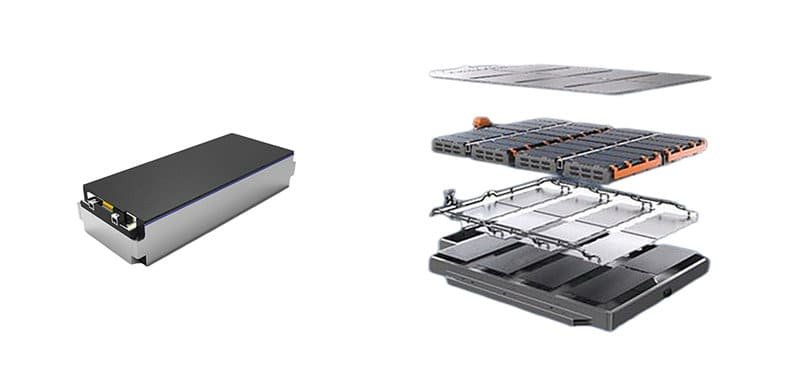
VDA Module VS MEB Platform
The MEB (Modular Electric Drive Matrix) platform is an electric vehicle platform developed by the Volkswagen Group and represents an important development direction in the modular design of contemporary electric vehicles. Designed to support different types of electric vehicles from compact cars to SUVs, the platform embodies the concept of modularity and standardization of electric vehicle platforms.
The battery system used in the MEB platform demonstrates the advantages of modular design. Its battery system design concept has some common ground with standardization ideas such as VDA, particularly in terms of modularity and standardization. This design allows the configuration of battery packs of different capacities on the same platform to meet the needs of different vehicle models.
Although the MEB and VDA modules share common principles, they also have different characteristics:
Similarities:
1.Modular design concept.
2.Standardized manufacturing processes.
3.Flexible product configuration.
4.Standardized safety standards.
Differences:
1.VDA is a wider industry standard designed to promote compatibility between different manufacturers.
2.Developed by the Volkswagen Group, MEB is its internal standard and is mainly used for electric vehicles under its brands.
VDA Battery Module Application
The electric vehicle sector is the most important application scenario for VDA battery modules. This standardized module design can be used for both pure electric vehicles and plug-in hybrids. In the commercial vehicle sector, including electric buses and logistics vehicles, VDA-compliant modules are also widely used due to their reliability and standardization.
In addition to electric vehicles, with the growing demand for large-scale energy storage systems, VDA modules are also frequently used in commercial energy storage systems, photovoltaic energy storage, grid peaking energy storage, and backup power for telecommunication base stations.
Conclusion
While VDA standard battery modules show significant benefits in many application scenarios, we recognize that not all projects are suitable. Some specific applications may have special needs. These needs are often difficult to meet with standardized modules.
For these special needs, our company provides professional customized services for battery modules. As a company focusing on battery technology, we can provide you with professional technical support and high quality product services, whether you need standard VDA modules or customized solutions. Our technical team can customize the most suitable solution for you according to your specific application scenario. If you are interested in our products and services, welcome to visit our website for more information, or contact our sales team directly: info@nbcell.com, we will be happy to provide you with professional technical support and detailed product information.