Lithium ion Battery Cooling System: Air Cooling vs. Liquid Cooling
With the rapid development of new energy industry, lithium ion batteries are more and more widely used in electric vehicles and energy storage systems. However, lithium ion batteries generate a lot of heat during the use process. If this heat is not emitted in time, it will not only affect the battery performance, but also may bring serious safety hazards.
According to research data, the optimal operating temperature range of lithium ion batteries is between 25-40℃, and the temperature difference inside the battery pack should be controlled within 5℃. When the temperature exceeds 50℃, the charging speed, efficiency and life of the battery will be significantly reduced. In some extreme cases, the high temperature may even trigger thermal runaway, leading to safety accidents!
Currently, the battery cooling solutions on the market include air cooling, liquid cooling, phase change material cooling and hybrid cooling, among which air cooling and liquid cooling are the two most common solutions. This article will explore the characteristics and applications of these two cooling technologies in depth.
Table of Contents
Air Cooling
Working Principle and System Composition
Air cooling technology is one of the earliest solutions used in lithium ion battery heat dissipation. It uses air as a heat dissipation medium and dissipates heat through three methods: heat conduction, heat convection, and heat radiation. From the realization of the way, air cooling system can be divided into two kinds: natural convection cooling and forced convection cooling.
Natural convection cooling is a passive heat dissipation method that relies on the natural flow of ambient air to carry away heat. This method has the simplest structure, but the heat dissipation effect is limited, and usually only suitable for applications with low heat generation.
Forced convection cooling uses fans, blowers or air conditioning units to generate forced airflow or low-temperature airflow to form an efficient heat exchange environment. In actual applications, suspended air-cooled air conditioners are more commonly used, while fans and blowers are less commonly used. A typical forced air cooling system includes the following core components:
- Cooling fan, blower or suspended air-cooled air conditioner.
- Air inlet and outlet duct system.
- Guide plate and wind shield.
- Temperature sensor network.
- Intelligent control system.
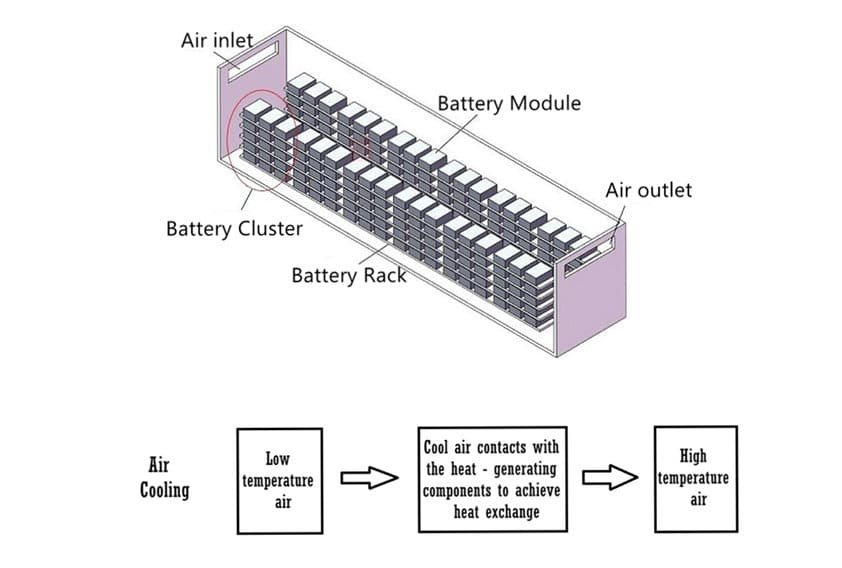
Advantages and Disadvantages of Air Cooling
Advantages
1. Simple and intuitive system structure, easy to install and maintain.
2. Low initial investment cost, good economy.
3. No risk of liquid leakage, high system safety.
4. Light weight system, low impact on overall quality.
5. low maintenance cost, simple operation.
Disadvantages
1. Relatively low heat dissipation efficiency (the specific heat capacity of air is only 1/4 of that of water).
2. Temperature control accuracy is limited, difficult to achieve particularly accurate temperature control.
3. Easily affected by the ambient temperature, the effect is not good in high temperature environment.
4. The fan will generate noise when running.
5. Insufficient heat dissipation may occur in high-power applications.
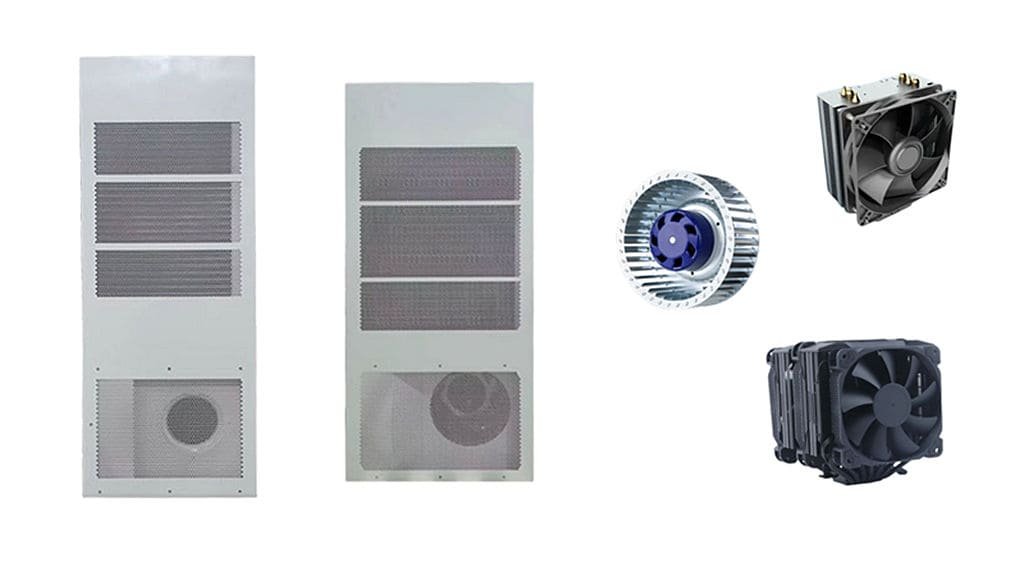
Optimization of Air Cooling Technology
In recent years, air cooling technology has been continuously improving, and the main optimization directions include three aspects:
1. Air Duct Design Optimization
The air duct is a key factor affecting the heat dissipation effect. Through computational fluid dynamics (CFD) analysis, engineers have developed a variety of innovative air duct design solutions. The optimized air duct can significantly improve the uniformity of airflow, reduce dead corners, and improve overall heat dissipation efficiency.
2. Improvement of Heat Dissipation Structure
Adding heat sinks, fins and other structures to the surface of the battery module can significantly increase the heat dissipation area. At the same time, by optimizing the shape and layout of these structures, more turbulence can be generated to improve heat exchange efficiency.
3. Intelligent Control Strategy
Modern air cooling systems generally use intelligent control strategies to dynamically adjust the fan speed according to battery temperature, ambient temperature, load conditions, etc. This ensures heat dissipation and reduces energy consumption.
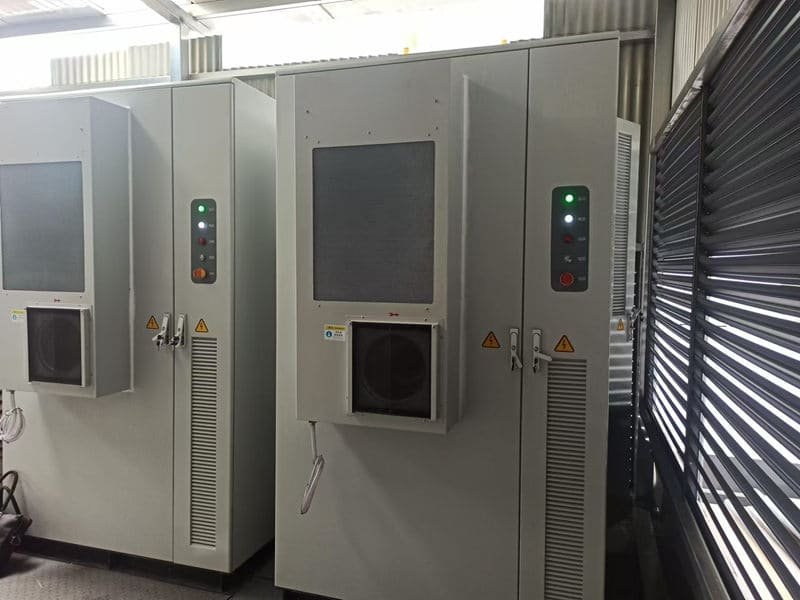
Liquid Cooling
Working Principle and System Composition
Liquid cooling technology uses liquid as a cooling medium to remove heat through the flow of liquid. Depending on how the coolant contacts the battery, liquid cooling systems can be divided into two types: indirect liquid cooling and immersion liquid cooling.
Indirect Liquid Cooling
Indirect liquid cooling is the most widely used liquid cooling method. It isolates the coolant from the battery through a special cooling plate or pipe. The coolant circulates in the pipe and carries away the heat generated by the battery through heat conduction.
A typical indirect liquid cooling system consists of the following main components:
- Coolant circulation system.
- Cold plate or pipe network.
- Heat exchanger.
- Circulation pump.
- Temperature sensor and control system.
Immersion Liquid Cooling
Immersion liquid cooling is a more radical heat dissipation solution. It immerses the battery directly in an insulating coolant to achieve direct contact heat dissipation. This method has a good heat dissipation effect, but it has extremely high requirements for the coolant, which needs to have excellent insulation, chemical stability and thermal conductivity. Later maintenance is difficult, and battery replacement is troublesome. Currently, there are few practical applications.
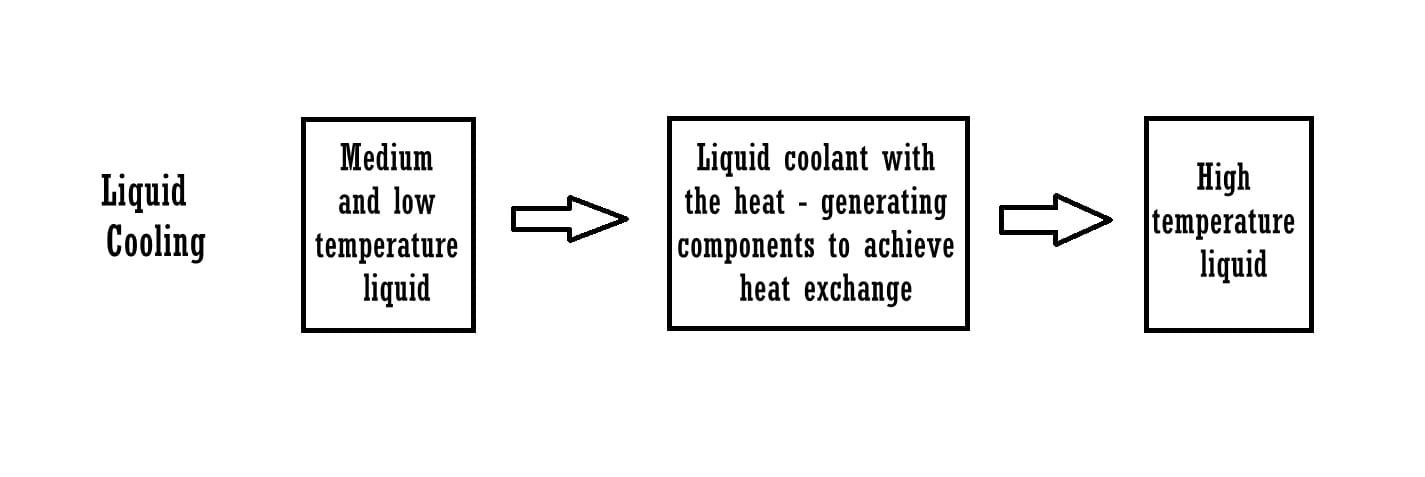
Advantages and Disadvantages of Liquid Cooling
Advantages
1. High heat dissipation efficiency, significant cooling effect.
2. Relatively accurate temperature control.
3. Even temperature distribution, beneficial to battery life.
4. Low system noise, good user experience.
5. Maintains good performance even in high temperature environment.
Disadvantages
1. Complex system structure.
2. High initial investment cost.
3. Risk of coolant leakage.
4. High maintenance requirements, requiring a professional team.
5. Higher system weight.
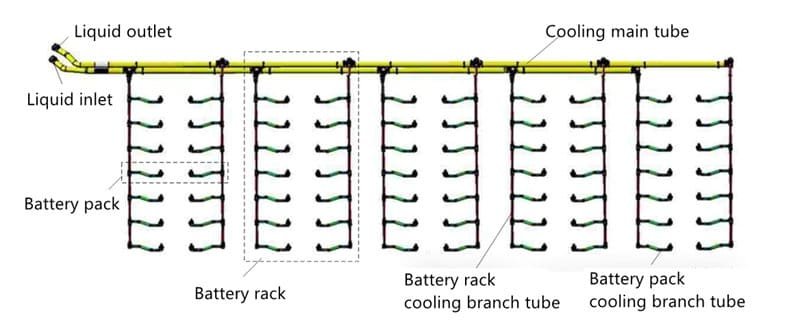
Optimization of Liquid Cooling Technology
In recent years, liquid cooling technology has made significant progress in many aspects:
1. Cooling Plate Design
There are many innovative cooling plate designs on the market, including:
- Parallel mini-channel cooling plate.
- Serpentine channel structure cooling plate.
- Streamlined channel cooling plate.
- Double-layer reverse channel cooling plate.
- Bionic wing vein cooling plate.
These different designs have their own characteristics and can meet the needs of different applications.
2. Coolant Optimization
The development of new coolants is also progressing. The ideal coolant should have:
- High thermal conductivity.
- Low electrical conductivity.
- Good chemical stability.
- Suitable viscosity.
- Low environmental impact.
3. Intelligent Temperature Control System
The advanced liquid cooling system uses intelligent control algorithms to:
- Real-time monitoring of temperature at each point.
- Dynamically adjust flow.
- Optimize energy consumption.
- Predict possible abnormalities.

Air Cooling vs. Liquid Cooling
Performance
The following is a performance comparison table of liquid cooling system and air cooling system:
Performance Indicator | Liquid Cooling System | Air Cooling System |
Maximum Temperature Control Range | 30-40℃ | 37-45℃ |
Temperature Difference Control Capability | ≤3℃ | ≤5℃ |
Heat Dissipation Efficiency | High | Medium |
Energy Consumption (relative value) | 1 | 2-3 times |
System Complexity | High | Low |
Maintenance Difficulty | High | Low |
Applications
Application of Air Cooling
Air cooling is mainly suitable for:
1. Small energy storage system.
2. Low energy density battery pack.
3. Applications with low charge and discharge rate.
4. Cost-sensitive projects.
5. Locations with limited maintenance conditions.
Application of Liquid Cooling
Liquid cooling system is more suitable for:
1. Large energy storage facilities.
2. High energy density battery packs.
3. Fast charging and discharging applications.
4. Use in high temperature environments.
5. Applications with high temperature control accuracy requirements.
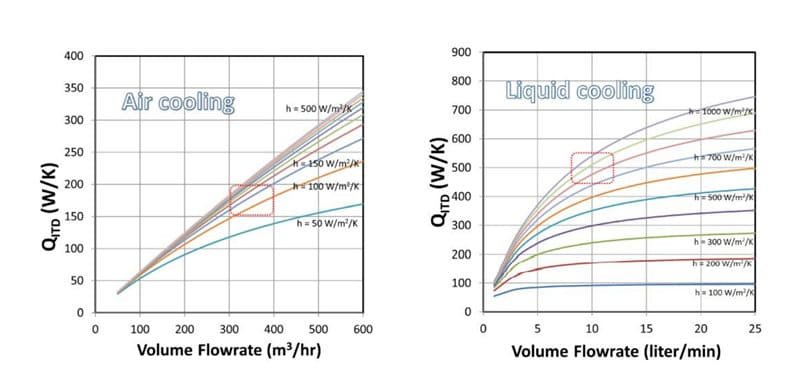
Other Cooling Technologies
In addition to air and liquid cooling, the industry is actively exploring other cooling solutions:
Phase Change Material (PCM) Cooling
Phase change material cooling uses the phase change process of the material to absorb heat, and has the characteristics of passive heat dissipation and temperature stability. It is currently mainly in the laboratory stage and has not yet been commercialized on a large scale.
Hybrid Cooling
Hybrid cooling combines the advantages of multiple cooling methods, such as air cooling + PCM, liquid cooling + PCM, etc. These technologies are under development and are expected to provide better heat dissipation solutions in the future.
Conclusion
With the development of the lithium ion battery industry, battery cooling technology is also constantly improving. Air cooling and liquid cooling each have their own advantages, and the appropriate solution needs to be selected according to the specific application.
In the short term, air cooling will still dominate in small and medium-sized applications due to its cost advantage. However, as technology advances and costs decrease, liquid cooling will be more widely used in large-scale energy storage.
In the future, with the development of new materials, new processes, and advancements in intelligent control technology, battery cooling technology will continue to evolve and provide better support for the development of the industry.