Haben Sie sich jemals gefragt, was Ihr Tesla- oder BYD-Elektrofahrzeug antreibt?? Da Elektroautos in unserem täglichen Leben immer häufiger vorkommen, Begriffe wie “Batteriezelle,” “Modul,” Und “Pack” tauchen häufig auf. Doch was genau bedeuten diese Begriffe?, und wie sie zusammenarbeiten, um Ihr Elektrofahrzeug anzutreiben?
Stellen Sie sich das wie Bauen mit LEGO-Steinen vor: Sie beginnen mit einzelnen Blöcken (Batteriezellen), Kombinieren Sie sie in kleinere Abschnitte (Batteriemodule), und schließlich eine vollständige Struktur erstellen (Akkupack). So wie jedes LEGO-Stück eine entscheidende Rolle bei der endgültigen Kreation spielt, Jede Ebene des Batteriesystems dient einem bestimmten Zweck bei der Stromversorgung Ihres Elektrofahrzeugs.
Werfen wir nun einen genaueren Blick auf die Batteriezelle, Modul und Paket, sowie die Verbindung und der Unterschied zwischen ihnen.
Inhaltsverzeichnis
Was ist eine Batteriezelle??
Eine Batteriezelle ist die grundlegendste Funktionseinheit einer Lithium-Ionen-Batterie. Betrachten Sie seine Struktur, Jede Batteriezelle enthält fünf Schlüsselkomponenten: eine positive Elektrode (Kathode), eine negative Elektrode (Anode), Elektrolyt, Separator, und Gehäuse. In der Kathode und Anode werden Lithiumionen gespeichert – Das Kathodenmaterial kann Lithiumkobaltoxid sein (LCO), Nickel-Kobalt-Mangan (NCM), oder Lithiumeisenphosphat (LFP), während die Anode typischerweise aus Graphitmaterialien besteht. Der Elektrolyt dient als Bewegungsbahn für Lithiumionen. Der Separator hat eine Doppelfunktion: Es verhindert den direkten Kontakt zwischen den positiven und negativen Elektroden und ermöglicht gleichzeitig den Durchgang von Lithiumionen. Endlich, Das Gehäuse bietet physischen Schutz und Abdichtung für die gesamte Batteriezelle.
Lithium-Ionen-Batteriezellen gibt es in drei Hauptformaten: zylindrisch, prismatisch, und Pouchzellen.
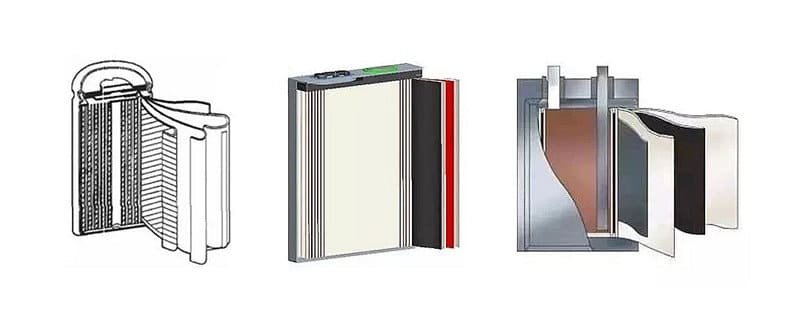
Zylindrische Batteriezelle
Zylindrische Batteriezellen waren die ersten Lithium-Ionen-Batterien, die in Massenproduktion hergestellt wurden. Sie werden durch Aufwickeln der Kathode hergestellt, Anode, und Separator in einer bestimmten Reihenfolge in eine Zylinderform bringen und dann in einem Metallgehäuse unterbringen. Zu den gängigsten Größen auf dem heutigen Markt gehören: 18650 (18mm Durchmesser, 65mm Länge, mit einer Kapazität von ca. 2,2-3,4Ah), 21700 (21mm Durchmesser, 70mm Länge, mit einer Kapazität von ca. 4,0-5,0Ah), und die neuere 4680 (46mm Durchmesser, 80mm Länge). Dank ihrer hervorragenden Zuverlässigkeit und Kostenvorteile, Zylindrische Batteriezellen werden häufig in Elektrowerkzeugen verwendet, tragbare Geräte, und Elektrofahrzeuge – wobei Tesla einer der größten Nutzer zylindrischer Batteriezellen ist.
Vorteile zylindrischer Batteriezellen
1. Ihr Herstellungsprozess ist der ausgereifteste und am höchsten automatisierte, Dies führt zu erheblichen Kostenvorteilen und einer gleichbleibenden Produktqualität.
2. Die zylindrische Form sorgt für eine gleichmäßige Spannungsverteilung bei Innendruck, Bietet hervorragende mechanische Festigkeit.
3. Hoher Standardisierungsgrad – Produkte verschiedener Hersteller sind austauschbar.
4. Großes Verhältnis von Oberfläche zu Volumen, Dadurch können sie die Wärme besser ableiten.
Nachteile zylindrischer Batteriezellen
1. Das auffälligste Problem ist ihre geringe Raumeffizienz. Zylindrische Formen erzeugen auf natürliche Weise Lücken, wenn sie in rechteckige Räume gepackt werden, was zu Platzverschwendung führt.
2. Aufgrund ihrer relativ geringen individuellen Kapazität, Um ein Batteriesystem mit hoher Kapazität zu schaffen, müssen viele Batteriezellen in Reihe und parallel geschaltet werden. Dadurch erhöht sich die Anzahl der Verbindungspunkte und die Montage wird komplexer.
3. Zylindrische Batteriezellen haben im Vergleich zu Pouch-Zellen typischerweise eine geringere Energiedichte, was ihren Einsatz in Anwendungen, die eine hohe Energiedichte erfordern, etwas einschränkt.
4. Ihre festen Abmessungen schränken die Gestaltungsfreiheit ein, Dies macht es schwierig, Batterieformen für bestimmte Anwendungen zu optimieren.
Prismatische Batteriezelle
Prismatische Batteriezellen verwenden als Gehäuse Hartschalen aus Aluminium oder Stahl, mit Innenstrukturen, die entweder im Wickel- oder Stapelverfahren hergestellt werden. Als gängiges Batterieformat, Prismatische Zellen bieten relativ flexible Abmessungen und größere Einzelkapazitäten, von 20Ah bis 314Ah, Einige Hersteller produzieren sogar 560-Ah-Batteriezellen. Momentan, Prismatische Zellen werden hauptsächlich in Elektrofahrzeugen eingesetzt, kommerzielle Elektrofahrzeuge, und Energiespeichersysteme. Große Batteriehersteller wie BYD, CATL und KAHL sind prismatische Zellen, die in Massenproduktion hergestellt werden.
Vorteile prismatischer Batteriezellen
1. Die rechteckige Struktur sorgt für eine bessere Raumausnutzung, trägt dazu bei, die Energiedichte von Batteriepacks zu erhöhen.
2. Die großen Kontaktflächen prismatischer Zellen erleichtern die Wärmeableitung, was sich positiv auf das Wärmemanagement der Batterie auswirkt.
3. Eine höhere Einzelzellenkapazität bedeutet weniger Reihen- und Parallelschaltungen im Vergleich zu zylindrischen Zellen, Vereinfachung des Systemdesigns.
4. Die großen ebenen Flächen erleichtern die Montage und Montage der Batterie.
Nachteile prismatischer Batteriezellen
1. Im Vergleich zu zylindrischen Zellen, Prismatische Zellen haben höhere Herstellungskosten und erfordern strengere Produktionsprozesse.
2. Aufgrund ihrer inneren Struktur, Prismatische Zellen neigen dazu, während der Lade- und Entladezyklen etwas aufzuquellen, erfordern zusätzlichen Platz und zusätzliche Einschränkungen bei der mechanischen Konstruktion.
3. Die Spezifikationen prismatischer Zellen variieren erheblich zwischen verschiedenen Herstellern in der Branche, Dies erschwert den Austausch zwischen verschiedenen Marken.

Beutelzelle
Pouch-Zellen verwenden als Außenhülle eine Aluminium-Kunststoff-Folie, typischerweise mit einer gestapelten Innenstruktur. Die Aluminium-Kunststoff-Folie besteht aus mehreren Schichten Verbundmaterialien, darunter Nylon, Aluminiumfolie, und Polypropylen, wodurch es leicht und kostengünstig ist. In der Unterhaltungselektronik, Pouchzellen gibt es in verschiedenen Größen und Kapazitäten, um den unterschiedlichen Produktanforderungen gerecht zu werden – Zum Beispiel, Smartphone-Akkus haben typischerweise Kapazitäten von 3–4 Ah, während Laptop-Akkus 5–8 Ah erreichen können. Momentan, Pouchzellen werden hauptsächlich in der Unterhaltungselektronik eingesetzt (wie Smartphones, Tabletten, und Laptops) und tragbare elektronische Geräte.
Vorteile von Pouchzellen
1. Dank ihres leichten Aluminium-Kunststoff-Foliengehäuses, Sie haben eine hohe gravimetrische Energiedichte (Energie pro Gewichtseinheit).
2. Pouch-Zellen bieten große Designflexibilität, Ermöglicht die Anpassung von Größe und Form an verschiedene Anwendungen.
3. Die gestapelte Innenstruktur sorgt für einen engen Kontakt zwischen den leitenden Schichten, Dies führt zu einem geringen Innenwiderstand und einer guten Geschwindigkeitsleistung.
4. Während des thermischen Durchgehens, Pouch-Zellen neigen dazu, den Innendruck durch Schwellung und Verformung abzubauen, statt eines gewaltsamen Explosionsversagens.
Nachteile von Pouchzellen
1. Das Aluminium-Kunststoff-Foliengehäuse weist eine relativ geringe mechanische Festigkeit auf und ist anfällig für äußere Beschädigungen, zum Schutz sind zusätzliche Strukturbauteile erforderlich.
2. Pouch-Zellen erfordern streng kontrollierte Herstellungsbedingungen, besonders empfindlich gegenüber Feuchtigkeit. Der Versiegelungsprozess muss in einer streng kontrollierten trockenen Umgebung durchgeführt werden.
3. Bei Lagerung und Transport ist besondere Vorsicht geboten, um Feuchtigkeit und physischen Druck zu vermeiden, was die Logistikkosten erhöht.
4. Beutelzellen weisen im Vergleich zu Hartschalenbatterien typischerweise geringere Produktionsausbeuten auf, was sich etwas auf ihre Kostenwettbewerbsfähigkeit auswirkt.
Was ist ein Batteriemodul??
Nach Einführung der kleinsten Einheit – die Batteriezelle – Lassen Sie uns die nächste Ebene eines Batteriesystems erkunden: Das Batteriemodul. Ein Batteriemodul ist eine Funktionseinheit, die durch Reihen- und Parallelschaltung mehrerer Batteriezellen entsteht. Es umfasst nicht nur die Batteriezellen selbst, sondern auch grundlegende elektrische Anschlüsse und Sicherheitsschutzfunktionen. Einfach gesagt, wenn Batteriezellen wie Bausteine sind, dann ist ein Batteriemodul die grundlegende Baueinheit aus diesen Blöcken.
Batteriemodule spielen eine entscheidende Zwischenrolle im gesamten Batteriesystem. Durch richtige Reihenschaltungen, Sie können die Spannung einer einzelnen Batteriezelle erhöhen (typischerweise 3,2–3,7 V) auf das erforderliche Niveau (wie 48V oder höher). Parallele Verbindungen erhöhen die Kapazität und Leistungsabgabemöglichkeiten. Über die Verbesserung der elektrischen Leistung hinaus, Beim Design von Batteriemodulen müssen mehrere technische Herausforderungen bewältigt werden, darunter auch das Ausbalancieren der Batteriezellen, Temperaturregelung, und strukturelle Unterstützung.
Für den Entwurf und die Anwendung des gesamten Batteriesystems ist ein umfassendes Verständnis der Batteriemodule unerlässlich. Wenn Sie mehr über Batteriemodule erfahren möchten, Lesen Sie gerne unseren speziellen Artikel: Was ist ein Batteriemodul??. In diesem Artikel finden Sie detailliertere Informationen zu Batteriemodulen.
Indem wir sowohl Batteriezellen als auch Batteriemodule verstehen, Wir haben den Grundstein für die Erforschung der Funktionsweise von Akkus und ihrer Designmerkmale gelegt. Ein Batteriepack integriert mehrere Batteriemodule zu einem vollständigen Energiespeichersystem. Fahren wir mit dem Lernen über Akkupacks fort.
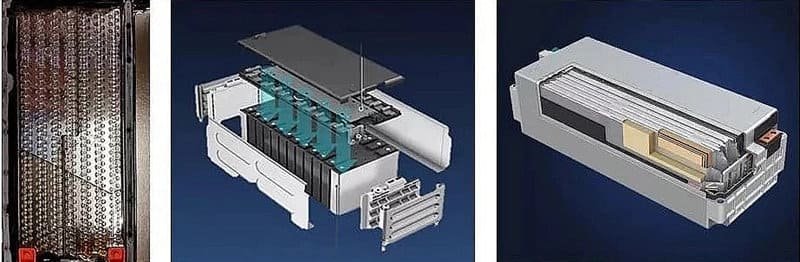
Was ist ein Akku??
Ein Batteriepack ist eine übergeordnete Energiespeichereinheit als ein Batteriemodul. Mehrere Batteriemodule werden über sorgfältig konzipierte Sammelschienensysteme in Reihe und parallel geschaltet, um die erforderlichen Spannungs- und Kapazitätsniveaus zu erreichen. Jedoch, Ein Batteriepack ist nicht nur eine einfache Kombination von Batteriemodulen – Es ist ein komplexes System. Ein komplettes Batteriepacksystem umfasst hauptsächlich: eine Reihe von Batteriemodulen, ein Batteriemanagementsystem (BMS), ein Wärmemanagementsystem (TMS), eine Hochspannungsverteilungseinheit, ein strukturelles Unterstützungssystem, und verschiedene Sensoren.
Die Konfigurationen von Akkupacks variieren je nach Anwendung erheblich. Bei Elektrofahrzeugen, Die Spannungen der Akkupacks liegen typischerweise zwischen 300 und 400 V (Einige High-End-Modelle verwenden 800-V-Systeme), und die Kapazitäten reichen von 30 kWh bis 100 kWh. Kommerzielle Elektrofahrzeuge erfordern möglicherweise noch größere Kapazitätsdesigns. Während in Energiespeicheranwendungen, Die Spanne reicht von wenigen kWh für die Energiespeicherung zu Hause bis hin zu Hunderten von MWh für die Speicherung auf Netzebene.
BMS
Das Batteriemanagementsystem (BMS) fungiert als “Gehirn” des Akkupacks. Es muss verschiedene Betriebsparameter in Echtzeit überwachen und verwalten, um einen sicheren und effizienten Systembetrieb zu gewährleisten. Ein vollständiges BMS umfasst typischerweise einen Master-Controller und mehrere Slave-Controller, Bildung einer hierarchischen Führungsstruktur. Der Master-Controller übernimmt die Verwaltung und Entscheidungsfindung auf Systemebene, während Slave-Controller auf Modulebene arbeiten, um detailliertere Daten zu sammeln.
Die Hauptaufgabe von BMS besteht darin, die Sicherheit des Batteriesystems zu gewährleisten. Dies geschieht durch die Überwachung der Spannung, aktuell, Temperatur, und andere Parameter in Echtzeit, um zu überprüfen, ob die Batterie innerhalb sicherer Grenzen arbeitet. Wenn eine Anomalie festgestellt wird, das BMS ergreift umgehend Schutzmaßnahmen, B. das Trennen des Hochspannungskreises oder das Aktivieren des Kühlsystems. Zusätzlich, Das BMS verwaltet die Vorladesteuerung, Während des Systemstarts wird durch eine Vorladeschaltung nach und nach eine Hochspannung aufgebaut, um Schäden an Komponenten durch Stromstöße zu verhindern.
Der Batteriezellenausgleich ist eine weitere wichtige Funktion des BMS. Während des Akkubetriebes, Einzelne Batteriezellen können aufgrund von Herstellungsschwankungen und unterschiedlichen Betriebsbedingungen Zustandsunterschiede entwickeln. Das BMS nutzt aktive oder passive Ausgleichstechniken, um den Ladezustand einzelner Batteriezellen anzupassen, um sicherzustellen, dass sie konsistent bleiben. Dies ist für die Maximierung der Lebensdauer und Leistung des Akkupacks von entscheidender Bedeutung.
Eine genaue Ladungsschätzung ist ebenfalls eine wichtige BMS-Aufgabe. Im Gegensatz zu Tankanzeigen in herkömmlichen Fahrzeugen, Schätzung des Ladezustands (SOC) und die verbleibende Reichweite bei Elektrofahrzeugen ist viel komplexer. Das BMS muss mehrere Faktoren berücksichtigen, einschließlich des Batteriestatus in Echtzeit, historische Nutzungsdaten, Umgebungstemperatur, und Fahrbedingungen, um genaue Schätzmodelle zu erstellen. Gleichzeitig, Es bewertet den Gesundheitszustand der Batterie (SOH) und prognostiziert Kapazitätsverschlechterungstendenzen, Bereitstellung wichtiger Informationen für Benutzer und Wartungspersonal.
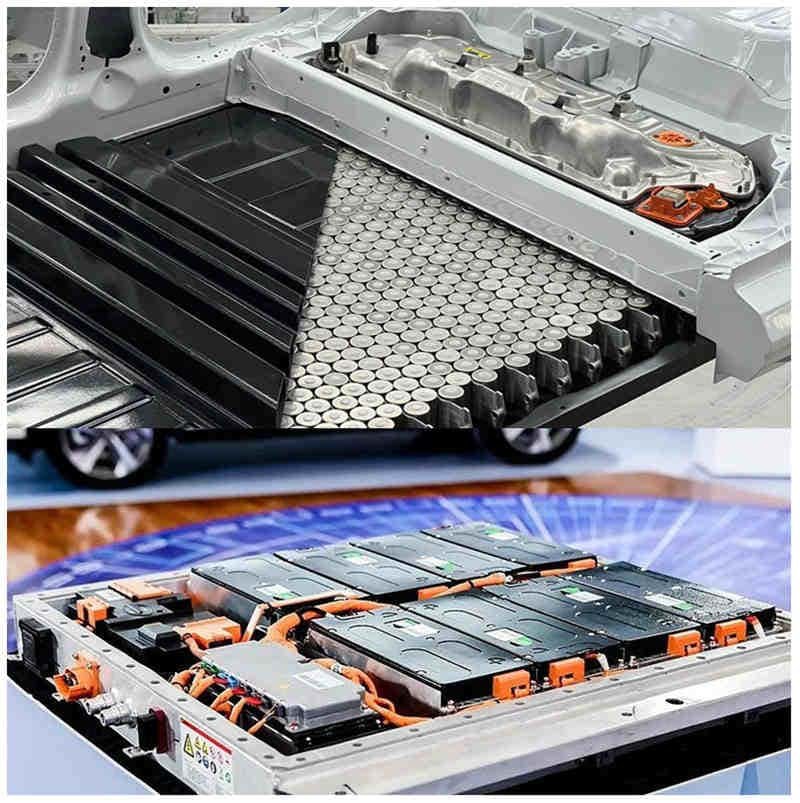
Wärmemanagementsystem
Das Wärmemanagementsystem (TMS) ist entscheidend für die Gewährleistung der Leistung und Sicherheit des Akkupacks. Lithiumbatterien erzeugen im Betrieb erhebliche Wärme, die, wenn sie nicht sofort verschwinden, verschwinden, kann nicht nur die Leistung beeinträchtigen, sondern auch zu Sicherheitsproblemen führen. Zu den aktuellen Mainstream-Wärmemanagementlösungen gehören:: Luftkühlsysteme, Flüssigkeitskühlsysteme, und Phasenwechselmaterial-Kühlsysteme. Bei Elektrofahrzeugen, Flüssigkeitskühlsysteme werden aufgrund ihrer hervorragenden Wärmeableitung und Platzeffizienz zur vorherrschenden Wahl. Für Energiespeichersysteme, Abhängig von den Kapazitätsanforderungen und der Betriebsumgebung können unterschiedliche Kühllösungen verwendet werden. Ein umfassendes Wärmemanagementsystem muss nicht nur die Kühlung, sondern auch die Heizung in kalten Umgebungen berücksichtigen – Dies ist für die Aufrechterhaltung der Lade-/Entladeleistung und Langlebigkeit des Akkus von entscheidender Bedeutung.
Sicherheitsschutz
Der Sicherheitsschutz ist ein entscheidender Faktor beim Design von Batteriepacks. Akkupacks erfordern mehrere Sicherheitsschutzmechanismen, einschließlich: elektrische Sicherheit, Schutz vor thermischem Durchgehen, und strukturelle Sicherheit. Für elektrische Sicherheit, Das Paket muss mit Hochspannungs-Trennvorrichtungen ausgestattet sein, Isolationsüberwachung, und Schutz vor Überladung und Tiefentladung. Zum Schutz vor thermischem Durchgehen, Das Design muss Barrieren zur Wärmeausbreitung umfassen, Warnsysteme, und Druckentlastungsgeräte. Was die strukturelle Sicherheit betrifft, Der Rucksack muss wasserdicht sein, Staubschutz, Vibrationsfestigkeit, und Aufprallschutz. Besonders im Automobilbereich, Akkupacks müssen strenge Crash-Sicherheitsstandards erfüllen.
Anwendungen
Batteriepacks haben unterschiedliche Designprioritäten für unterschiedliche Anwendungen.
Bei Elektrofahrzeugen, Die Anpassung des Batteriepakets an das gesamte Fahrzeugsystem ist ein komplexer Prozess. Zuerst kommt die mechanische Integration – Der Batteriesatz muss eng in die Fahrzeugkarosserie integriert sein, Erfüllt sowohl den Platzbedarf als auch die Gewährleistung von Strukturfestigkeit und Crashsicherheit. Als nächstes kommt die elektrische Integration, Dies erfordert eine Abstimmung mit den Hochspannungs- und Ladesystemen des Fahrzeugs. Dann gibt es noch die Integration des Wärmemanagements, das für eine effiziente Temperaturregelung mit der Klimaanlage des Fahrzeugs zusammenarbeiten muss. Endlich, Faktoren wie Fahrzeuggewichtsverteilung und Kostenkontrolle müssen berücksichtigt werden. Elektro-Personenfahrzeuge verwenden typischerweise a “Skateboard” Design, Integration des Akkupacks unter das Chassis – Dies senkt den Schwerpunkt für ein besseres Handling und maximiert die Raumnutzung im Fahrzeug.
In Energiespeicheranwendungen, Die Prioritäten bei der Konstruktion von Batteriepacks unterscheiden sich von denen bei Anwendungen in Elektrofahrzeugen. Im Vergleich zum Einsatz von Elektrofahrzeugen, Bei Energiespeicherbatterien liegt der Schwerpunkt mehr auf der Skalierbarkeit des Systems, Zyklus Leben, und Wirtschaftlichkeit, Gleichzeitig gelten entspanntere Anforderungen an Leistungsdichte und Volumenbeschränkungen. Große Energiespeicherstationen verwenden typischerweise Container-basierte Designs, organische Kombination mehrerer Batteriepacksysteme mit unabhängigen Brandschutz- und Umweltkontrollsystemen. Zusätzlich, Energiespeicherbatteriepakete erfordern spezielle Energiemanagementsysteme (EMS) Lade-/Entladestrategien zu optimieren, Verbesserung der Systemökonomie, und die Betriebskosten senken.
Unterschiede zwischen Batteriezellen, Modul und Paket
Die Beziehung zwischen Batteriezellen, Module, und Packen ist nicht nur ein einfacher Stapelvorgang, sondern das Ergebnis umfassender Betrachtungen einschließlich der Performance, Sicherheit, und Kostenfaktoren. Betrachten wir die Unterschiede und Zusammenhänge zwischen diesen drei Ebenen aus unterschiedlichen Perspektiven.
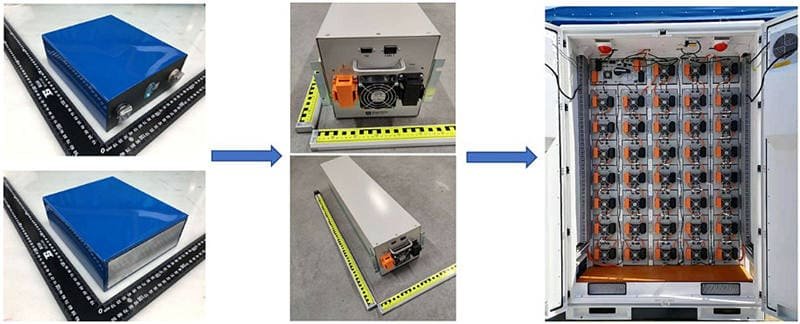
Funktional
Aus funktionaler Sicht, Jede Ebene hat ihren eigenen Schwerpunkt. Als Grundeinheit, Batteriezellen dienen in erster Linie der Umwandlung zwischen elektrochemischer und elektrischer Energie, Speicherung und Freisetzung von Energie durch interne elektrochemische Reaktionen. Batteriemodule dienen hauptsächlich der effektiven Verbindung von Batteriezellen, Bereitstellung grundlegender elektrischer Verbindungen und mechanischer Unterstützung, und bietet gleichzeitig einen vorläufigen Schutz für die Batteriezellen. Das Batteriepaket ist ein Komplettsystem, das nicht nur Energie speichert, sondern auch Funktionen auf Systemebene implementiert, einschließlich eines umfassenden Batteriemanagements, Wärmemanagement, und Sicherheitsschutz.
Leistung
In Bezug auf die Leistungsmerkmale, Es gibt deutliche Unterschiede zwischen den drei Ebenen. Einzelne Batteriezellen arbeiten typischerweise mit Spannungen zwischen 3,2 und 3,7 V, mit Kapazitäten von wenigen bis mehreren hundert Amperestunden. Ihre Leistungsmerkmale bestimmen die Kernkompetenzen des gesamten Energiespeichersystems. Zum Beispiel, Die Energiedichte einer Batteriezelle wirkt sich direkt auf die Reichweite des Systems aus, während seine Ratenfähigkeit die Lade- und Entladegeschwindigkeit bestimmt.
Batteriemodule kombinieren mehrere Batteriezellen in Reihe und parallel, um höhere Spannungen und größere Kapazitäten zu erreichen. Zusätzlich, Batteriemodule bieten strukturelle Unterstützung, um sicherzustellen, dass Batteriezellen richtig ausgerichtet und sicher befestigt sind. Batteriemodule integrieren außerdem grundlegende Spannungserkennungs- und Temperaturüberwachungsfunktionen. Noch wichtiger, Beim Design des Batteriemoduls müssen die Kühlanforderungen berücksichtigt werden, typischerweise mit speziellen Kühlkanälen oder Kühlplatten. Alle diese Designelemente bilden den Grundstein für die Systemintegration auf Batteriepaketebene.
Batteriepacks enthalten nicht nur mehrere Batteriemodule, sondern integrieren auch komplette BMS- und Wärmemanagementsysteme. Daher, Ihr hervorstechendes Merkmal ist die Systemvollständigkeit und umfassende Funktionalität.
Aufgrund der zunehmenden Anzahl von Hilfskomponenten auf jeder Ebene, Die Energiedichte nimmt von Batteriezellen über Batteriemodule bis hin zu Batteriepaketen allmählich ab. Nehmen wir als Beispiel eine konkrete NCM-Batterie, Die Energiedichte der Batteriezelle kann 260 Wh/kg erreichen, Die Energiedichte des Batteriemoduls beträgt etwa 230 Wh/kg, während der Akku auf etwa 190 Wh/kg sinkt.
Kostenstruktur
Auch in der Kostenstruktur gibt es erhebliche Unterschiede. In den Gesamtkosten für den Akku, Batteriezellen machen mit rund 10 % den größten Anteil aus 50%, wobei Kathodenmaterialien den Hauptkostenbestandteil der Batteriezellen darstellen. Auf Batteriemodulebene, Kostensteigerungen durch Strukturbauteile und Anschlüsse. Der Batteriepack-Level erhöht die Systemkosten für das BMS, Wärmemanagement, und Bautenschutz. Diese Kostenverteilung zeigt, dass die Reduzierung der Batteriezellenkosten der Schlüssel zur Verbesserung der Wirtschaftlichkeit des gesamten Energiespeichersystems ist.
Angesichts des technologischen Fortschritts ist dies erwähnenswert, Die traditionelle dreistufige Struktur entwickelt sich weiter. Zum Beispiel, Einige Hersteller haben CTP eingeführt (Cell-to-Pack) Technologie, was das Traditionelle vereinfacht “Zellmodulpaket” Hierarchie durch direkten Übergang von Zelle zu Packung. Diese Innovation bringt zwar Verbesserungen in der Energiedichte mit sich, es stellt auch höhere Anforderungen an Design- und Herstellungsprozesse.
Abschließend, Es ist wichtig, den SOC und SOH der Batterie zu kennen. Für Benutzer, Sie können den Status der Batterie erfassen und diese besser nutzen und warten. Für Hersteller, Sie können ihre Produkte und Technologien kontinuierlich aktualisieren, um leistungsstärkere Batterien herzustellen.