Ever wondered what powers your Tesla or BYD electric vehicle? As electric cars become increasingly common in our daily lives, terms like “battery cell,” “module,” and “pack” pop up frequently. But what exactly do these terms mean, and how do they work together to power your EV?
Think of it like building with LEGO bricks: you start with individual blocks (battery cells), combine them into smaller sections (battery modules), and finally create a complete structure (battery pack). Just as each LEGO piece plays a crucial role in the final creation, each level of the battery system serves a specific purpose in powering your electric vehicle.
Now let’s take a deeper look at battery cell, module and pack, as well as the connection and difference between them.
Table of Contents
What is Battery Cell?
A battery cell is the most basic functional unit of a lithium-ion battery. Looking at its structure, each battery cell contains five key components: a positive electrode (cathode), a negative electrode (anode), electrolyte, separator, and casing. The cathode and anode are where lithium ions are stored – the cathode material can be lithium cobalt oxide (LCO), nickel-cobalt-manganese (NCM), or lithium iron phosphate (LFP), while the anode is typically made of graphite materials. The electrolyte acts as a pathway for lithium ions to move around. The separator has a dual role: it prevents direct contact between the positive and negative electrodes while allowing lithium ions to pass through. Finally, the casing provides physical protection and sealing for the entire battery cell.
Lithium-ion battery cells come in three main formats: cylindrical, prismatic, and pouch cells.
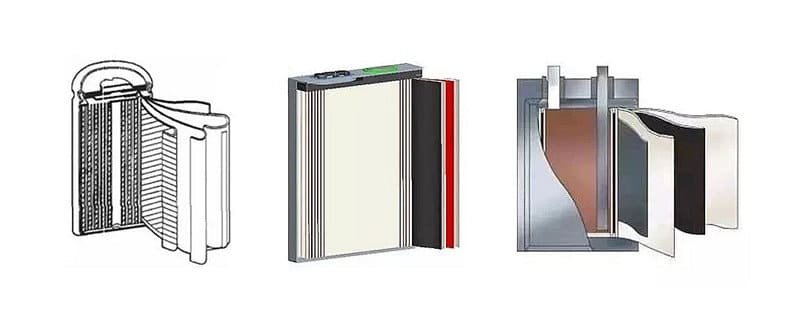
Cylindrical Battery Cell
Cylindrical battery cells were the first lithium-ion batteries to achieve mass production. They’re made by winding the cathode, anode, and separator in a specific order into a cylinder shape and then housing it in a metal casing. The most common sizes on the market today include 18650 (18mm diameter, 65mm length, with a capacity of about 2.2-3.4Ah), 21700 (21mm diameter, 70mm length, with a capacity of about 4.0-5.0Ah), and the newer 4680 (46mm diameter, 80mm length). Thanks to their excellent reliability and cost advantages, cylindrical battery cells are widely used in power tools, portable devices, and electric vehicles – with Tesla being one of the largest users of cylindrical battery cells.
Advantages of Cylindrical Battery Cells
1. Their manufacturing process is the most mature and highly automated, leading to significant cost benefits and consistent product quality.
2. The cylindrical shape ensures even stress distribution when under internal pressure, providing excellent mechanical strength.
3. High degree of standardization – products from different manufacturers are interchangeable.
4. Large surface area-to-volume ratio, which makes them better at heat dissipation.
Disadvantages of Cylindrical Battery Cells
1. The most notable issue is their low space efficiency. Cylindrical shapes naturally create gaps when packed into rectangular spaces, resulting in wasted space.
2. Due to their relatively small individual capacity, creating a high-capacity battery system requires connecting many battery cells in series and parallel. This increases the number of connection points and makes assembly more complex.
3. Cylindrical battery cells typically have lower energy density compared to pouch cells, which somewhat limits their use in applications requiring high energy density.
4. Their fixed dimensions limit design flexibility, making it difficult to optimize battery shapes for specific applications.
Prismatic Battery Cell
Prismatic battery cells use aluminum or steel hard cases for housing, with internal structures made using either winding or stacking processes. As a mainstream battery format, prismatic cells offer relatively flexible dimensions and larger individual capacities, ranging from 20Ah to 314Ah, with some manufacturers even producing 560Ah battery cells. Currently, prismatic cells are mainly used in electric vehicles, commercial EVs, and energy storage systems. Major battery manufacturers like BYD, CATL and CALB are mass-producing prismatic cells.
Advantages of Prismatic Battery Cells
1. The rectangular structure provides better space utilization, helping to increase the energy density of battery packs.
2. The large contact surfaces of prismatic cells make heat dissipation easier, which is beneficial for battery thermal management.
3. Higher individual cell capacity means fewer series and parallel connections compared to cylindrical cells, simplifying system design.
4. The large flat surfaces make battery mounting and assembly more convenient.
Disadvantages of Prismatic Battery Cells
1. Compared to cylindrical cells, prismatic cells have higher manufacturing costs and require more stringent production processes.
2. Due to their internal structure, prismatic cells tend to swell somewhat during charging and discharging cycles, requiring extra space and additional constraints in mechanical design.
3. Prismatic cell specifications vary significantly among different manufacturers in the industry, making it difficult to interchange between different brands.

Pouch Cell
Pouch cells use aluminum-plastic film as their outer casing, typically with a stacked internal structure. The aluminum-plastic film is made of multiple layers of composite materials including nylon, aluminum foil, and polypropylene, making it lightweight and cost-effective. In consumer electronics, pouch cells come in various sizes and capacities to meet different product requirements – for example, smartphone batteries typically have capacities of 3-4Ah, while laptop batteries can reach 5-8Ah. Currently, pouch cells are mainly used in consumer electronics (such as smartphones, tablets, and laptops) and portable electronic devices.
Advantages of Pouch Cells
1. Thanks to their lightweight aluminum-plastic film casing, they have high gravimetric energy density (energy per unit weight).
2. Pouch cells offer great design flexibility, allowing customization of size and shape for different applications.
3. The stacked internal structure creates tight contact between conductive layers, resulting in low internal resistance and good rate performance.
4. During thermal runaway, pouch cells tend to release internal pressure through swelling and deformation, rather than violent explosive failure.
Disadvantages of Pouch Cells
1. The aluminum-plastic film casing has relatively low mechanical strength and is vulnerable to external damage, requiring additional structural components for protection.
2. Pouch cells require highly controlled manufacturing conditions, being particularly sensitive to moisture. The sealing process must be done in a strictly controlled dry environment.
3. Special care is needed during storage and transportation to prevent moisture exposure and physical pressure, which increases logistics costs.
4. Pouch cells typically have lower production yield rates compared to hard-case batteries, which somewhat affects their cost competitiveness.
What is Battery Module?
After introducing the smallest unit – the battery cell – let’s explore the next level in a battery system: the battery module. A battery module is a functional unit made by connecting multiple battery cells in series and parallel. It includes not only the battery cells themselves but also basic electrical connections and safety protection features. Simply put, if battery cells are like building blocks, then a battery module is the basic structural unit made from these blocks.
Battery modules play a crucial intermediate role in the overall battery system. Through proper series connections, they can boost the voltage of a single battery cell (typically 3.2-3.7V) to required levels (such as 48V or higher). Parallel connections increase capacity and power output capabilities. Beyond improving electrical performance, battery module design must address multiple technical challenges including battery cell balancing, temperature control, and structural support.
A thorough understanding of battery modules is essential for the design and application of the entire battery system. If you’d like to learn more about battery modules, feel free to read our dedicated article: what is a battery module?. This article provides more detailed information about battery modules.
By understanding both battery cells and battery modules, we’ve laid the groundwork for exploring how battery packs work and their design features. A battery pack integrates multiple battery modules to form a complete energy storage system. Let’s continue with learning about battery packs.
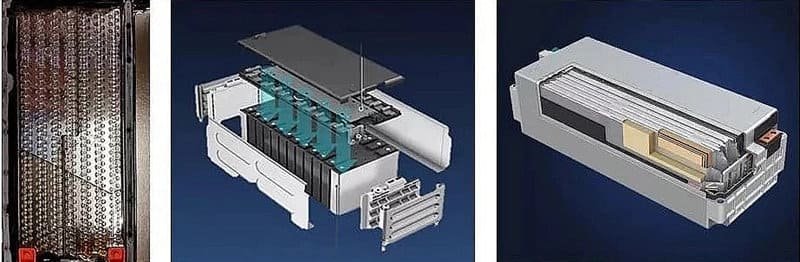
What is Battery Pack?
A battery pack is a higher-level energy storage unit than a battery module. Multiple battery modules are connected in series and parallel through carefully designed busbar systems to achieve the required voltage and capacity levels. However, a battery pack isn’t just a simple combination of battery modules – it’s a complex system. A complete battery pack system mainly includes: an array of battery modules, a Battery Management System (BMS), a Thermal Management System (TMS), a high-voltage distribution unit, a structural support system, and various sensors.
Battery pack configurations vary significantly depending on their application. In electric vehicles, battery pack voltages typically range from 300-400V (with some high-end models using 800V systems), and capacities range from 30kWh to 100kWh. Commercial EVs might require even larger capacity designs. While in energy storage applications, the range extends from a few kWh for home energy storage to hundreds of MWh for grid-level storage.
BMS
The Battery Management System (BMS) acts as the “brain” of the battery pack. It needs to monitor and manage various operating parameters in real-time to ensure safe and efficient system operation. A complete BMS typically includes a master controller and multiple slave controllers, forming a hierarchical management structure. The master controller handles system-level management and decision-making, while slave controllers work at the module level to collect more detailed data.
The primary task of BMS is ensuring battery system safety. It does this by monitoring voltage, current, temperature, and other parameters in real-time to verify that the battery is operating within safe limits. If any abnormality is detected, the BMS immediately takes protective measures, such as disconnecting the high-voltage circuit or activating the cooling system. Additionally, the BMS manages pre-charge control, gradually building up high voltage through a pre-charge circuit during system startup to prevent damage to components from current surges.
Battery cell balancing is another crucial function of the BMS. During battery pack operation, individual battery cells may develop state differences due to manufacturing variations and different operating conditions. The BMS uses active or passive balancing techniques to adjust the charge state of individual battery cells, ensuring they remain consistent. This is vital for maximizing battery pack lifespan and performance.
Accurate charge estimation is also a key BMS task. Unlike fuel gauges in traditional vehicles, estimating the State of Charge (SOC) and remaining range in electric vehicles is much more complex. The BMS must consider multiple factors including real-time battery status, historical usage data, ambient temperature, and driving conditions to build accurate estimation models. Simultaneously, it evaluates the battery’s State of Health (SOH) and predicts capacity degradation trends, providing important information for users and maintenance personnel.
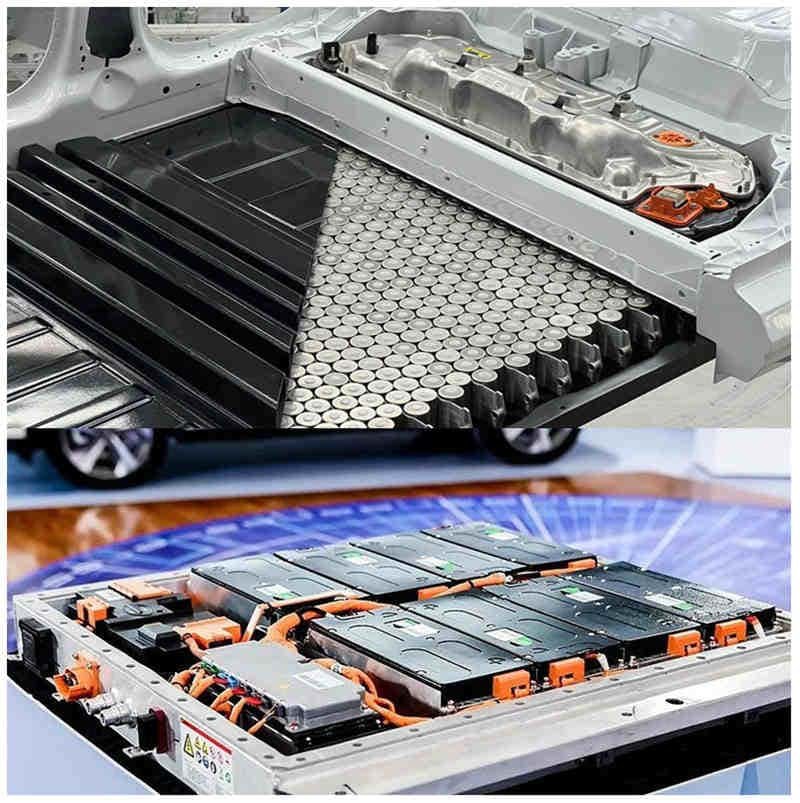
Thermal Management System
The Thermal Management System (TMS) is crucial for ensuring battery pack performance and safety. Lithium batteries generate significant heat during operation, which if not dissipated promptly, can not only affect performance but also lead to safety issues. Current mainstream thermal management solutions include: air cooling systems, liquid cooling systems, and phase-change material cooling systems. In electric vehicles, liquid cooling systems are becoming the dominant choice due to their excellent heat dissipation and space efficiency. For energy storage systems, different cooling solutions may be used depending on capacity requirements and operating environment. A comprehensive thermal management system must consider not only cooling but also heating in cold environments – this is essential for maintaining battery charging/discharging performance and longevity.
Safety Protection
Safety protection is a critical factor in battery pack design. Battery packs require multiple safety protection mechanisms, including: electrical safety, thermal runaway protection, and structural safety. For electrical safety, the pack must be equipped with high-voltage disconnection devices, insulation monitoring, and protection against overcharging and over-discharging. For thermal runaway protection, the design must include thermal propagation barriers, warning systems, and pressure relief devices. As for structural safety, the pack needs to be designed for water resistance, dust protection, vibration resistance, and crash protection. Particularly in automotive applications, battery packs must meet stringent crash safety standards.
Applications
Battery packs have different design priorities for different applications.
In electric vehicles, matching the battery pack with the overall vehicle system is a complex process. First comes mechanical integration – the battery pack needs to be highly integrated with the vehicle body, meeting both space requirements and ensuring structural strength and crash safety. Next is electrical integration, requiring coordination with the vehicle’s high-voltage and charging systems. Then there’s thermal management integration, which needs to work with the vehicle’s air conditioning system for efficient temperature control. Finally, factors like vehicle weight distribution and cost control must be considered. Electric passenger vehicles typically use a “skateboard” design, integrating the battery pack under the chassis – this both lowers the center of gravity for better handling and maximizes vehicle space utilization.
In energy storage applications, battery pack design priorities differ from electric vehicles applications. Compared to electric vehicles use, energy storage battery packs focus more on system scalability, cycle life, and cost-effectiveness, while having more relaxed requirements for power density and volume constraints. Large energy storage stations typically use container-based designs, organically combining multiple battery pack systems with independent fire protection and environmental control systems. Additionally, energy storage battery packs require specialized Energy Management Systems (EMS) to optimize charging/discharging strategies, improve system economics, and reduce operating costs.
Differences between Battery Cell, Module and Pack
The relationship between battery cells, modules, and packs isn’t just a simple stacking process, but rather the result of comprehensive considerations including performance, safety, and cost factors. Let’s examine the differences and connections between these three levels from different perspectives.
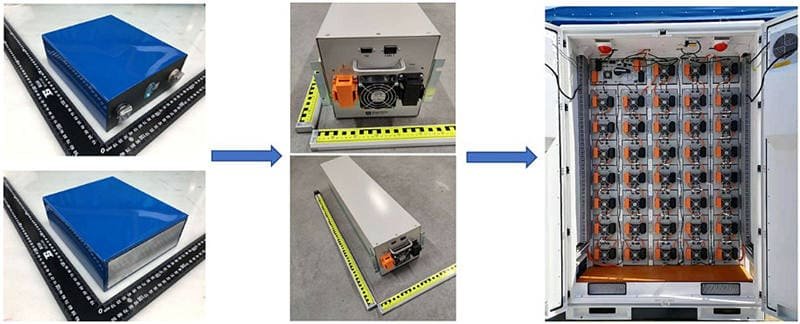
Functional
From a functional perspective, each level has its own focus. As the basic unit, battery cells primarily function to convert between electrochemical and electrical energy, storing and releasing energy through internal electrochemical reactions. Battery modules mainly serve to effectively combine battery cells, providing basic electrical connections and mechanical support, while offering preliminary protection for the battery cells. The battery pack is a complete system that not only stores energy but also implements system-level functions including comprehensive battery management, thermal management, and safety protection.
Performance
In terms of performance characteristics, there are clear differences between the three levels. Individual battery cells typically operate at voltages between 3.2-3.7V, with capacities ranging from a few to several hundred ampere-hours. Their performance characteristics determine the core capabilities of the entire energy storage system. For example, a battery cell’s energy density directly affects the system’s range, while its rate capability determines charging and discharging speeds.
Battery modules combine multiple battery cells in series and parallel to achieve higher voltages and larger capacities. Additionally, battery modules provide structural support to ensure battery cells are properly aligned and securely fixed. Battery modules also integrate basic voltage detection and temperature monitoring functions. More importantly, battery module design must consider cooling requirements, typically incorporating dedicated cooling channels or cooling plates. All these design elements lay the foundation for system integration at the battery pack level.
Battery packs not only contain multiple battery modules but also integrate complete BMS and thermal management systems. Thus, their most distinctive feature is system completeness and comprehensive functionality.
Due to the increasing number of auxiliary components at each level, energy density gradually decreases from battery cells to battery modules to battery packs. Taking a specific NCM battery as an example, battery cell energy density can reach 260Wh/kg, battery module energy density is around 230Wh/kg, while the battery pack drops to about 190Wh/kg.
Cost Structure
There are also significant differences in cost structure. In the total battery pack cost, battery cells account for the largest portion at around 50%, with cathode materials being the main cost component of the battery cells. At the battery module level, costs increase due to structural components and connectors. The battery pack level adds system costs for BMS, thermal management, and structural protection. This cost distribution indicates that reducing battery cell costs is key to improving the economics of the entire energy storage system.
It’s worth noting that with technological advancements, the traditional three-level structure continues to evolve. For example, some manufacturers have introduced CTP (Cell-to-Pack) technology, which simplifies the traditional “cell-module-pack” hierarchy by going directly from cell to pack. While this innovation brings improvements in energy density, it also places higher demands on design and manufacturing processes.
In conclusion, it is important to know the SOC and SOH of the battery. For users, they can grasp the status of the battery and use and maintain it better. For manufacturers, they can continuously update their products and technologies to produce better performing batteries.